Roles and Responsibilities
User
It is the prime responsibility of the user to keep the instrument in a valid state of control. Utilization procedures with training records of users to operate the instrument must be in place.
Quality Unit
It is the responsibility of the quality unit to ensure that the AIQ process meets all compliance requirements and that all AIQ process requirements are being followed. Complete, valid and documented data of the AIQ process must be maintained.
Manufacturers/Suppliers/Service/Agents/Consultants
It is the responsibility of the manufacturer to design and manufacture the instrument, and to ensure that the instrument is manufactured and assembled by using relevant quality processes. The assembled instrument should be tested by the manufacturer before shipment. Necessary specifications (e.g. configuration and design specifications) should be developed for the user for ready reference and to compare with the user requirements. There should be a signed contract (quality or technical agreement) between the user organization (contract giver) and the service provider (contract accepter) in which the scope of work and responsibility of each party should be defined.
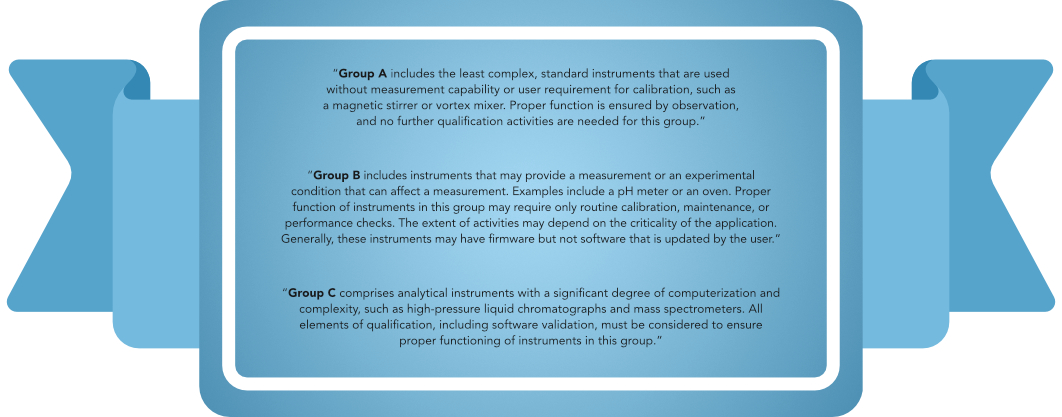
Decision Tree for classification of an analytical instrument:
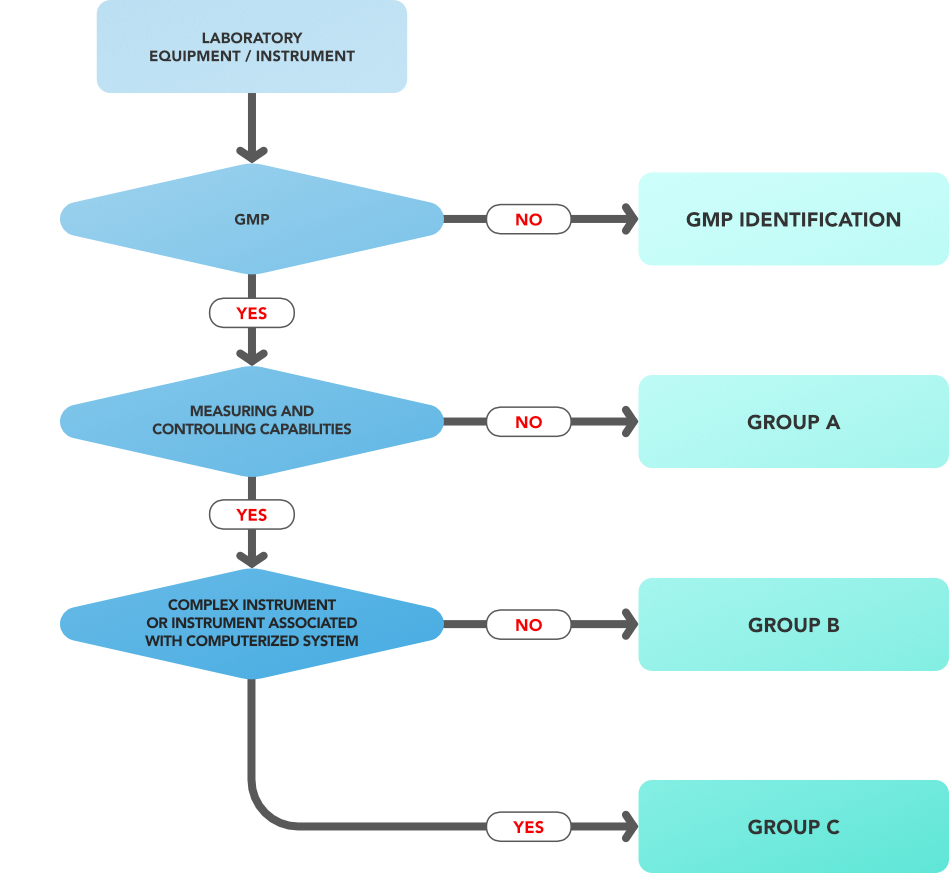
Qualification Type:
- A prospective qualification is performed on new instruments. It is carried out before a product has been tested on the instrument. It can also be done when a significant change to the instrument or analysis has been made that may affect the analytical results.
- A retrospective qualification is performed on instruments which are in use and the related activity is carried out when the system’s intended usage has already started.
Analytical Instrument Qualification (Qualification Phases)
Some analytical instrument qualification activities cover more than one qualification phase, and the user could potentially perform them during more than one of the phases. However, there is a need for a logical, specific order to the qualification activities. All qualification activities should be predefined and contemporaneously documented.
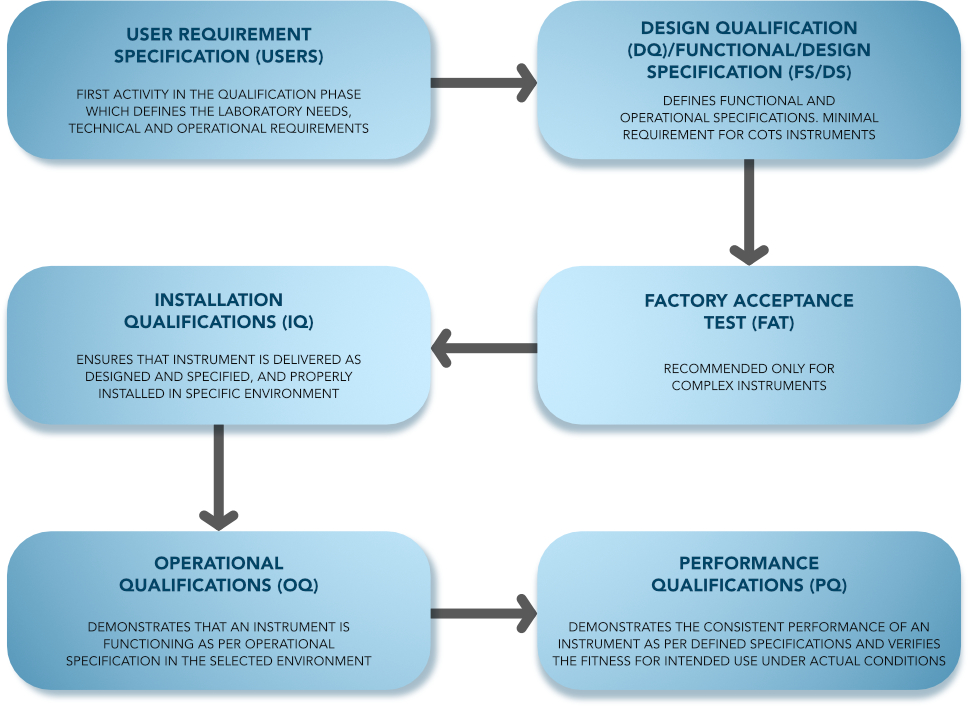
Documents generated during qualification activities should be retained in an accessible manner. Where multiple instruments of one kind exist, documents common to all instruments and documents specific to an instrument should be stored separately. Additional documents may supplement those obtained during the re-qualification process, and both sets of documents should be retained and maintained in a suitable manner that allows for appropriate protection and access.
Summary
The goal of Commissioning and Qualification of Laboratory Instruments is to ensure that the instrument is fully compliant with regulations. The GMP requirement in combination with measurement capability, controlling ability, analytical process involvement, data criticality and instrument complexity become the base for Analytical Instruments Qualification using risk-based scientific approaches to ensure it is acceptable to use in a GMP environment.
References
- USP Chapter <1058>, Analytical Instrument Qualification
- ISPE Baseline® Guide, Commissioning and Qualification (Volume 5)